Движущая сила «Нижнекамскнефтехима»
Сильной стороной ПАО «Нижнекамскнефтехим» по праву можно назвать наличие в его составе производства этилена. Это так называемая базовая нефтехимия. В конце августа уникальному этиленовому комплексу исполнилось 40 лет. В РФ аналогов этому производству по мощностям с самого его основания в 1976 году и по сегодняшний день пока не существует. О значимости олефинов, а также о том, как все начиналось, дне сегодняшнем и перспективах производства этилена на «Нижнекамскнефтехиме» узнавал корреспондент «Реального времени».
Он сложный самый…
«Пускались, скорее, мы методом «тыка», на ошибках. Хотя коллектив был и большой, почти тысяча человек, но опытных спецов, так сказать, «гигантов мысли», как сегодня, почти не было», — вспоминает о том, как пускался завод этилена его ветеран Юрий Спиридонов, который устроился на Нижнекамский химкомбинат в сентябре 1975 года.
Этиленовый комплекс «Нижнекамскнефтехима» — производство уникальное. Таковым его окрестили еще в 70-е годы из-за того, что размер производства не соответствовал объемам выпускаемой продукции: проектная мощность завода в 450 тыс. тонн многократно превышала единственное в то время производство этилена в башкирском Салавате, а все установки производственного комплекса уместились, можно сказать, на площадке всего в 250 тыс. кв. метров.
А началось все в конце 60-х годов с контракта, подписанного между всесоюзным объединением «Техмашимпорт» и фирмой Toyo Engineering на проектирование и поставку оборудования для этиленового комплекса. Решение о строительстве комплекса производств этилена, пропилена, дивинила, бензола и других сопутствующих продуктов в Нижнекамске было принято на самом высоком уровне — ЦК КПСС и Советом министров СССР — в декабре 1970 года. В 1973—1974 годах на территории химкомбината развернулось широкомасштабное строительство, и уже в июне 1976 года был получен первый товарный этилен.
Пик работ пришелся на 1975-й: строительная площадка тогда напоминала большой муравейник, она была плотно заполнена кранами и людьми, численность строителей и монтажников порой здесь достигала 9 тысяч человек в день. Завод был построен в рекордно короткие сроки: монтаж основного оборудования занял всего 14 месяцев, а вот от первоначальной даты намеченного пуска до реального запуска производства в эксплуатацию прошло целых 8 месяцев.
Пуск был очень тяжелым, подчеркивают те, кто участвовал в нем. Главная проблема в большей степени была связана с нехваткой опытных специалистов, хотя на пусковой объект и прибыли механики и технологи из разных уголков Союза. Запустить самый крупный этиленовый комплекс в стране планировали, как было принято в те годы в СССР, к очередной годовщине октябрьской революции, которую праздновали 7 ноября. «Уже висит лозунг, что-то вроде «Дадим стране...», мы тут пускаемся, тут и там идет монтаж, ставятся колонны. Думаю, неужели через месяц все это смонтируется? И все-таки мы не пустились на ноябрьские, и правильно, наверное, сделали: зима была суровой, а японцы, как известно, очень щепетильны, докапывались до каждой мелочи, поэтому мы досконально все доводили до ума. Так и дотянули до середины мая, пускались долго и нудно. Видимо, такого классного опыта, чтобы нас поставить на путь истинный, у японцев тоже не было. Хватались, помнится, они за головы, садились в кружки, кумекали по-своему», — рассказывает Юрий Спиридонов.
Немало проблем в этот пусковой период добавили компрессоры японской компании Mitsubishi. Запустили их только специалисты, командированные в Нижнекамск с завода этилена в Салавате, когда японские инженеры уже разошлись по домам, глубокой ночью. «Японцы приходят — оборудование работает. Пустились и тут же встали. Вообще, остановов в те годы было много, текучесть на заводе была высокой — многие не выдерживали такого темпа», — рассказывают те, кто работают на заводе с самого его основания.
«Сложность доставил и языковой барьер, было много технических инструкций на японском, так вот, сначала с японского переводили на английский, потом с английского — на русский. Сейчас читаешь эти инструкции, — говорит Спиридонов, — ну что за галиматья написана, а пускать-то завод надо было». Но в итоге образовался основной костяк завода, появились лидеры, старшие аппаратчики и машинисты, которые смогли привести всю технологическую документацию в порядок.
«Столько не написал Ленин томов, сколько Геннадий Иванович написал различных регламентов по ведению технологического процесса, — шутит над своим коллегой Геннадием Шуниным, с которым бок о бок трудится со дня пуска завода Юрий Спиридонов, — не дай Бог, упадет нечаянно на ногу, точно перелом будет».
21 июня 1976 года произошло событие, которого нефтехимики и вся страна ждали почти три года — был получен первый продуктовый этилен. Как с улыбкой сегодня вспоминают ветераны завода, «первый полученный этилен в мешочки грузили». Акт приемки этиленового производства в эксплуатацию государственная комиссия подписала 31 августа. Эта дата и стала официальным днем рождения завода.
Однако в стабильный режим завод вошел только в середине 80-х годов. При проектной мощности в 450 тыс. тонн завод выдавал по 200—300 тыс. тонн этилена в год, поскольку Нижнекамский химкомбинат к тому времени сам еще был не готов переработать почти полумиллионный объем олефинов. Поэтому практически весь этилен отправлялся на казанский «Оргсинтез» для получения полиэтиленовой пленки. Сегодня же каждая тонна этилена и других продуктов пиролиза, которые выпускает завод — на вес золота.
За четыре десятка лет, с момента ввода завода в эксплуатацию и по сегодняшний день, этиленовый комплекс ПАО «Нижнекамскнефтехим» произвел более 16 млн тонн этилена, около 8 млн тонн пропилена, более 2 млн тонн дивинила и более 6 млн тонн бензола.
Через огонь, воду и медные трубы
«Становление и дальнейшее развитие этилена — это становление поколения, как говорят на «Нижнекамскнефтехиме», этиленщиков. А так как производство этилена очень сложное, — замечает директор производства Ильгиз Яруллин, который пришел на завод в начале 90-х годов, — то и работники здесь очень грамотные, особенно ИТР, которые обучают основам технологического процесса молодежь, приходящую после техникумов и вузов. Много зависит и от аппаратчиков и машинистов, к которым на заводе очень высокие требования».
Да и как не быть всем этим жестким требованиям, если приходится обслуживать самое главное оборудование комплекса — печи, температура внутри которых достигает 1200 градусов, а в цехе, где работают компрессоры, наоборот, криогенный холод — минус 160 градусов. Вдобавок ко всему — легкие углеводороды, которыми наполнены колонны установок, — опасный, легковоспламеняющийся продукт.
Сегодня средний возраст коллектива завода в 565 человек — 36 лет. За последние годы произошло его значительное омоложение — средний возраст снизился на четыре года. Тренд этому был задан в 2003 году, когда генеральный директор «Нижнекамскнефтехима» Владимир Бусыгин поручил управление самым сложным заводом на предприятии 34-летнему Азату Бикмурзину, который до этого руководил одним из цехов. Тогда он стал самым молодым директором завода за всю историю предприятия. Многие сомневались: «А справится ли такой молодой? Выдержит ли нагрузку?». Но справился достойно и даже больше — с 2014 года Азат Бикмурзин возглавляет одну из крупнейших в стране нефтехимических компаний.
До Бикмурзина долгие годы заводом управлял Хамит Гильманов, начинавший здесь с главного механика. Затем он стал главным инженером и первым заместителем генерального директора «Нижнекамскнефтехима». Ему на смену пришел тоже бывший этиленщик — Ильфат Шарифуллин, прошедший путь от машиниста компрессоров, начальника установки, начальника цеха до директора завода этилена.
Как подчеркивает нынешний директор комплекса Ильгиз Яруллин, «наш завод — настоящая кузница кадров. Здесь работники проходят и огонь, и воду, и медные трубы».
Славится завод и своими семейными династиями. Одна из них — Закировы, отец и два сына. Устроившись в середине 70-х годов на строящийся завод этилена, Галимзян Закиров и не думал, что его выбор станет определяющим в судьбе всей его семьи. Здесь он встретил свою любовь, появилась семья, родились двое сыновей. Причем оба выбрали нефтехимическую специальность без долгих и мучительных раздумий. Перед их глазами всегда был яркий пример отца. «У нас на заводе за один год аппаратчиком не становишься. Ими становятся только года через 3—4», — подчеркивает сложность производства его директор.
Если раньше на заводе очень много зависело от самого человека, то проблемы, которые возникали тогда, сейчас нивелирует современная техника — за человека думает машина. «Есть и такие машины, которые просто не позволяют ошибиться, если обслуживающий персонал производит некорректные действия», делятся старожилы производства.
Эпоха цифровых машин, микропроцессорная система управления пришла на завод вместе с модернизацией основного оборудования — печей. Новейшая техника японской фирмы «Йокогава» сделала технологический процесс более надежным. До этого его вели с помощью пневматических приборов, щитовой системы управления. Все параметры персоналу приходилось держать в голове, и порой человеческий фактор играл тут не самую лучшую роль. Сейчас же умные машины сами подсказывают, где произошел сбой.
Курс — на увеличение
Основа основ — так об этилене скажет любой нефтехимик-профессионал. Этот продукт — своего рода производная для изготовления сотен других нефтехимических продуктов. И сегодня он востребован как никогда. При этом объемы производства этилена в России в два раза меньше, чем даже в Иране.
В 70-е годы этиленовый комплекс Нижнекамского химкомбината задумывался как гигантское по тем временам производство мощностью 450 тысяч тонн продукции в год. Однако многие годы на этих нагрузках нефтехимики не работали. Столько этилена не требовалось.
Так было вплоть до конца 90-х годов. Тогда руководство предприятия приняло ряд стратегических решений, направленных на увеличение выпуска основных видов продукции — каучуков и ряда мономеров. Тем более в рамках стратегии развития предприятие планировало переход от производства мономеров — к полимерам, подразумевавший возведение заводов по выпуску пластиков — полиэтилена, полипропилена, полистирола. Основополагающим сырьем в производстве которых были продукты, получаемые на этиленовом заводе. Имеющихся объемов производства олефинов на них точно уже не хватало.
В 2001 году стартовала очередная модернизация и реконструкция этиленового комплекса НКНХ. Цель стояла амбициозная — достичь годового объема в 600 тыс. тонн этилена. К ее реализации привлекли американскую компанию ABB Lummus Global. В рамках разработанной программы предстояло заменить практически все печи и другое значимое технологическое оборудование. Практически каждый год в технологическую цепочку включалось новое оборудование — печи пиролиза, компрессоры, турбины. Был смонтирован и ряд установок.
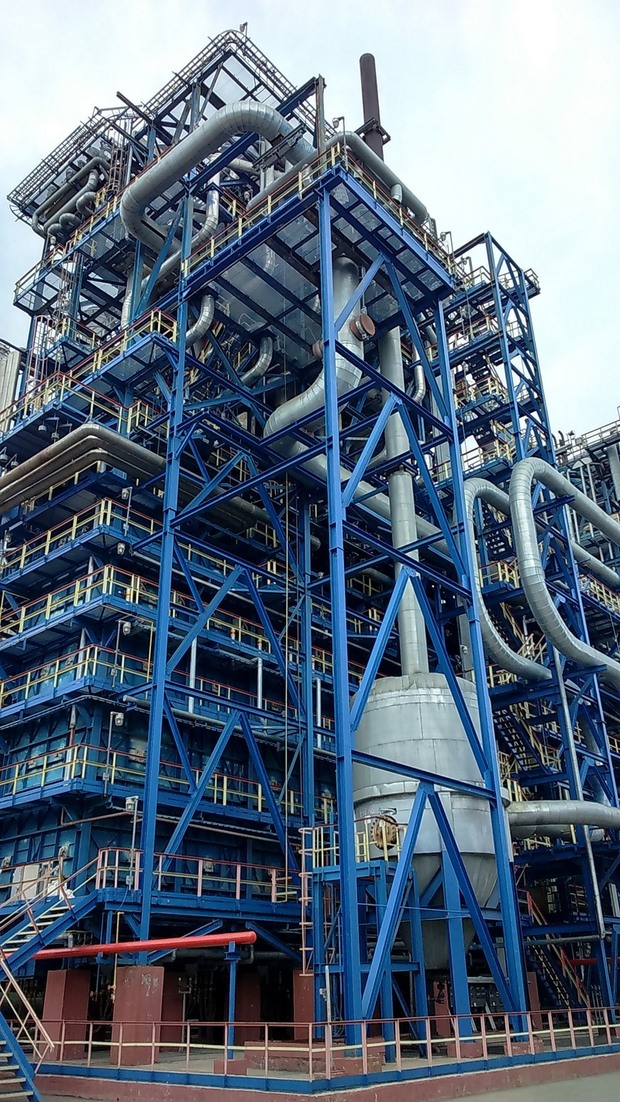
Модернизация на заводе проходила без прекращения выпуска продукции. Самым сложным было разместить новое оборудование и реконструировать существующее на такой маленькой площадке, тем более сроки на проведение капитальных ремонтов отводились довольно сжатые. Как отмечает директор завода Ильгиз Яруллин, «здесь невозможно просто взять остановить завод и спокойно менять оборудование. Объяснить это можно, прежде всего, высокой востребованностью этилена и пропилена».
Капремонт за капремонтом нефтехимики обновляли оборудование этиленового комплекса. На площадке появились новые технологические узлы. Модернизация была поэтапной и длилась почти 10 лет.
Первого результата от проводимой модернизации завод достиг в 2005 году, когда была получена рекордная за 30 лет существования завода выработка продукции: 465 тысяч тонн этилена и 203 тысячи тонн пропилена. В 2010 году заводчане достигли нового уровня — без малого 593 тыс. тонн продукции и 13 млн тонн с момента пуска производства. И наконец, спустя год, в 2011-м, завод пришел к заветному рубежу в 600 тыс. тонн продукции, к которому стремился с 2001 года.
За это время на территории комплекса были возведены шесть новых печей пиролиза: две газовых, остальные для пиролиза бензина и бутана. Причем проект каждой был выполнен специально для нижнекамского этиленового комплекса. Кстати, первая в те годы в России печь типа SRT-6 была смонтирована и запущена в производство именно на «Нижнекамскнефтехиме».
Увеличение объемов этилена способствовало наращиванию и других видов продукции на НКНХ. Как отметил в одном из интервью председатель совета директоров «Нижнекамскнефтехима» Владимир Бусыгин, «этилен является сердцем всего нашего комбината. Без этилена немыслимо производство полиэтилена, полипропилена, каучука — прежде всего, наращивание каучука. И без фракций, которые получает завод, не было бы такого наращивания по производству ГБК и БК».
Между тем в планах у завода построить еще две печи пиролиза. Кроме того, одна из важных на сегодняшний день задач — увеличить производство бензола, востребованного на заводах стирола и полиэфирных смол и других производствах «Нижнекамскнефтехима».
В единой технологической цепочке
Увидеть и пощупать этилен невозможно — это бесцветный газ. Впервые он был получен в 1680 году немецким химиком Иоганном Бехером, а сегодня этилен — самое производимое органическое соединение в мире, поскольку является одним из базовых продуктов промышленной химии. В природных газах этилен не встречается, поэтому был налажен индустриальный способ его получения. Он образуется сложным путем разложения углеводородов при высокой температуре в печах.
Безусловно, самым впечатляющим зрелищем для человека, далекого от нефтехимии и впервые попавшего на завод, — это печи пиролиза. Огромные, высотой больше 40 метров, они являются главной частью технологического процесса получения этилена. В них при температуре 850 градусов на составные части разделяется прямогонный бензин.
Новые печи, смонтированные в рамках модернизации завода, с точки зрения технологии являются высокопроизводительными, высокоселективными и «гибкими», то есть могут работать как на газовом, так и на жидком сырье — прямогонном бензине.
В цепочке, состоящей из девяти заводов «Нижнекамскнефтехима», производство этилена является, по сути, головным — это сырьевой источник, без которого не сможет функционировать ни один другой завод. Здесь производятся необходимые для выпуска каучуков дивинил и изобутиленовая фракция, этилен и пропилен для выпуска пластиков. «100% продукции востребовано и не копится на складах», — говорит о значимости своего производства Ильгиз Яруллин. Сегодня в ассортименте товарной продукции компании — 120 наименований и практически в каждом есть доля продукции, которую делает завод этилена.
Завод пластиков, пожалуй, самый активный потребитель олефинов: на него уходит львиная доля этилена и пропилена, из которых, в свою очередь, получают полимеры этилена и пропилена. Помимо собственного обеспечения, продукция служит сырьем для производств «Казаньоргсинтеза», отправляется по этиленопроводу в Башкортостан — Уфу, Салават и Стерлитамак.
Но прежде чем попасть к потребителям, этилен проходит через сложный производственный цикл. Это порядка 100 различных технологических процессов, каждый из которых имеет свои тонкости. И если хотя бы в одном из звеньев произойдет сбой, то разрушится вся технологическая цепочка.
Этилен будущего
Дальнейшая стратегия развития нефтехимического флагмана Татарстана связана с реализацией проекта по возведению нового этиленового комплекса и интегрированных в него заводов по изготовлению самых востребованных видов пластиков. По своим масштабам он станет, по сути, третьей промышленной зоной «Нижнекамскнефтехима».
Во время визита на «Нижнекамскнефтехим» в апреле этого года президент РТ Рустам Минниханов назвал олефиновый комплекс «главной задачей для компании и РТ, поскольку именно НКНХ является точкой роста в Камском кластере по нефтехимии и нефтепереработке». Он отметил, что если в рамках программы увеличения выпуска каучуков у компании все решается, то для развития пластиков нужен этилен. «Строительство этиленового комплекса является самой приоритетной программой Камского кластера», — подчеркнул президент.
Что касается дальнейшей судьбы действующего уже 40 лет завода этилена, то годовой объем продукции в 610 тыс. тонн, которого он достиг на сегодняшний день, — максимум, отметил директор комплекса Ильгиз Яруллин. Поэтому руководством компании и было принято стратегическое решение — строить новый комплекс. Но новый олефиновый комплекс не станет заменой имеющемуся: совместно с ним «Нижнекамскнефтехим» сможет к 2026 году получать почти 2 млн тонн этилена. А богатый опыт специалистов завода этилена уже сейчас служит опорой в решении актуальных вопросов, связанных с различными техническими вопросами в ходе реализации главного проекта «Нижнекамскнефтехима».
Подписывайтесь на телеграм-канал, группу «ВКонтакте» и страницу в «Одноклассниках» «Реального времени». Ежедневные видео на Rutube, «Дзене» и Youtube.