«Целились в океан, попали в медицину»: татарстанские судостроители пустят титан на импланты
Зеленодольский завод им. Горького освоил технологию производства титанового порошка, от которого зависят производители имплантов по аддитивным технологиям
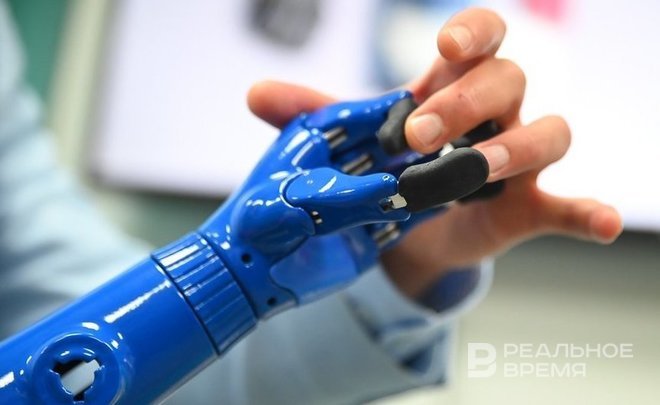
«Титановый эндопротез весом всего 200 граммов вернет человеку возможность ходить, зубной имплант — жевать, а замена «позвонка» спасет ему жизнь», — рассказывает главный металлург Зеленодольского завода им. Горького Марат Саубанов. Четыре года назад татарстанские судостроители в экспериментальном порядке взялись за освоение производства титанового порошка, необходимого для прямого выращивания имплантов при помощи 3D-печати. Как стало известно «Реальному времени», у предприятия есть масса титанового порошка для выращивания протезов в 3D-печати и наработки в этой сфере, однако инвестировать в производство протезов там пока не готовы — нет твердых заказов и господдержки.
Приготовить титановый порошок и «залить»
Зеленодольские судостроители, строящие из титана и алюминия огромные боевые корабли, не остановились на сухом исполнении ГОЗ и вступили в кооперацию с медицинской наукой и бизнесом. В партнерстве с российскими компаниями Зеленодольский завод им. Горького изготовил опытные образцы эндопротезов, выращенные из титанового порошка собственного производства. Впервые их коллекция была показана на недавней выставке V лидер-форума «Аддитивные технологии — новая реальность», организованного «Росатомом» в Казани.
Рядом с каждым эндопротезом стояла колба с титановой смесью — то, из чего был произведен каждый экспонат. Их мало кто замечал, ведь сами по себе титановые порошки не являются конструкционным материалом, это лишь сырьевой полупродукт. Но от порошковой металлургии зависят все игроки на рынке аддитивных технологий. Видимо, по этой причине СК «Ак Барс» взялась за разработку собственного способа получения титанового порошка. К тому же титан остается одним из самых дорогостоящих материалов, поэтому не каждый сможет его покупать для научных экспериментов и производить из него порошки для 3D-печати.

— Литье конструкционных фасонных отливок из титановых сплавов мы ведем более 50 лет. На заводе работает самая мощная в стране печь по титановому литью «Нева-5». Так что нашим металлургам пришлось на практике изучить свойства титановых сплавов и технологические тонкости. Но практическое применение нашли им и в медицине, — рассказал «Реальному времени» главный металлург Зеленодольского завода им. Горького Марат Саубанов.
По его словам, рабочая группа предприятия за несколько лет разработала собственную технологию получения титанового порошка из металла. Тут и потребовалась двухтонная печь «Нева-5», где происходит распыление титана под давлением газа. В печи металл плавится, а затем измельчается на кристаллы, превращаясь в порошок. Затем титановые порошки проходили тестовую экспертизу на промышленном 3D-принтере. По словам Марата Саубанова, тестовые испытания проходили в московском институте «Прометей», а затем в лаборатории КФУ. В обоих были получены положительные результаты. А технология изготовления титановых порошков запатентована в Роспатенте. Одним словом, целились в океан, попали в медицину.
«Судостроительный профиль не меняем, но титан пробуем в медицине»
Титан — бесценный для медицины материал. Импланты из него быстро приживаются в человеческом организме и не вызывают отторжения. Ни медь, ни железо и никакой другой материал не может органично «раствориться» в человеке.
— У нас есть разные образцы имплантов, — подтвердил технический директор СК «Ак Барс» Олег Варфоломеев (акционер завода). — Конечно, мы выращивали их не сами, а обращались к партнерам. Прежде чем приобретать промышленный 3D-принтер, надо не только его изучить, но и иметь «полезные» для него порошки, — уверен он.
В результате первые эндопротезы были выпущены на чужих принтерах. Зато завод убедился в пригодности титановых порошков и научился изготавливать несколько видов.

«Судостроительный профиль мы не меняем, но теперь титан интересует нас и для медицинских изделий», — заверил Варфоломеев. Ведь с уходом иностранных поставщиков имплантов потребность в титановых порошках в медицинской промышленности будет расти, прогнозирует он.
Пойдет ли «Ак Барс» с заявкой в «Росатом»?
Будет ли «Ак Барс» выходить с заявкой в «Росатом» с созданием центра аддитивных технологий? «Говорить о том, что завтра мы выходим на создание центра аддитивных технологий, наверное, было бы преждевременно, — заявил технический директор СК «Ак Барс». — Во-первых, мы не знаем потребности рынка на сегодняшний день. Хотя многие говорят, что это хорошее, перспективное направление. Но всегда нужно считать, каким будет экономический выхлоп от вложенных инвестиций», — рассуждает Варфоломеев .
Во-вторых, государственная поддержка в выведении на рынок новых продуктов медицинского назначения должна быть больше, полагает он. Предстоящее субсидирование НИОКР в пропорции 50 на 50 недавно анонсировал директор по технологическому развитию госкорпорации «Росатом» Андрей Шевченко. По его словам, в федеральном правительстве обкатывается проект комплексной научно-технологической программы, которая компенсирует предприятиям расходы на НИОКР. Предполагаемая стоимость — 20 млрд рублей. Механизм КНТП обеспечивает интерфейс между наукой и промышленностью.
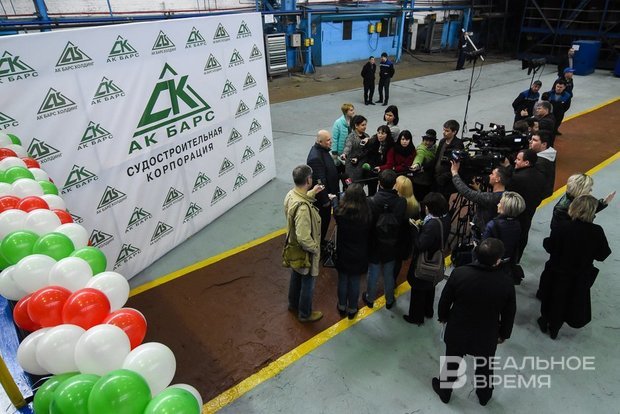
— Вообще, КНТП предназначена для того, чтобы вывести продукты на рынок. Здесь 50% расходов оплачивает государство в виде НИОКР, а остальные 50% — частные инвестиции на сам продукт, — рассказывал он в разговоре с «Реальным временем».
Эта пропорция не совсем устроит производителей, работающих по 44-ФЗ (по госзаказу). Почему? «Если по старой ФЦП мы «заходили» на объекты по модернизации и техническому перевооружению в соотношении 60 на 40, то сейчас — 90 на 10».
— Субсидия в 50% для предприятия, работающего в рамках 44-ФЗ, наверное, это хорошее вливание. Но лучше бы, если бы сделали соотношение 80 на 20 или 90 на 10. Ну посудите сами, необязательно быть великим финансистом или бизнесменом. Начать разработку, вложив 50% расходов и не имея контрактов под реализацию, — это значит «заморозить» деньги, — рассуждает технический директор СК «Ак Барс».
С другой стороны, мы хорошо понимаем, что страна находится в режиме СВО. Если бы была другая обстановка, то условия были бы более благоприятные.
Как «узаконить» выращенные комплектующие
В-третьих, серьезным барьером для внедрения АТ остаются нормативные регламенты, запрещающие самостоятельно менять технологию выпуска. Главная проблема в том, что нужно узаконить в машиностроении и судостроении изделия, которые выращены по аддитивным технологиям. Комплектующие из АТ не пройдут сертификацию речного регистра, и уже тем более военную приемку. Испытания, проверки, согласования — все это потребует немало времени. Придется пройти долгий путь по вхождению в программу комплектации того или иного машиностроительного изделия. Те компании, которые приобрели 3D-принтеры, до сих пор проходят путь по сертификации изделий.
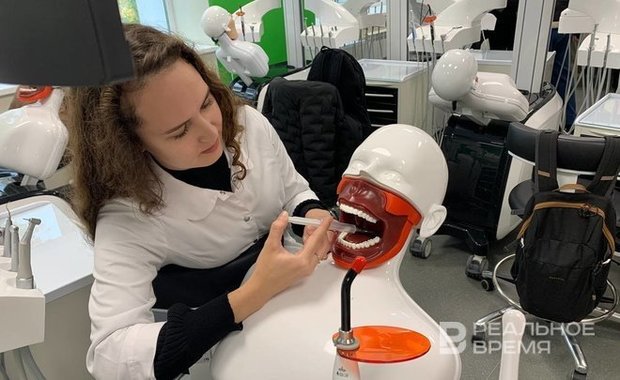
«Мы с этой проблемой знакомы не понаслышке, — признает технический директор СК «Ак Барс». — Когда строили первое СПГ-судно, пришлось проходить разрешительные процедуры за короткие сроки. Не во всех регламентах было прописано, что речное судно на СПГ-топливе может ходить по российским рекам. Сейчас они плавают только потому, что мы подключились и внесли немало изменений в нормативные документы о том, что речные суда на новом виде топлива могут эксплуатироваться по воде в России, а не только по автомобильным дорогам. Нам пришлось пройти долгий путь, чтобы внести изменения в требования речного регистра», — говорит Варфоломеев.
«Если нет заказов, значит, «заморозим» деньги в 3D-печати»
Пока СК «Ак Барс» приценивается к аддитивным технологиям. «У нас есть потенциальный партнер, потенциальный заказчик, но заказов нет. Маркетологи держат паузу. Все говорят, что это правильно и перспективно, но пока нет полной уверенности. Когда у нас будет пакет заказов, тогда можно будет говорить о каких-либо изделиях. Тогда будем выносить этот вопрос на совет директоров. А вкладывать инвестиции, не имея пакета контрактов, — это уже не бизнес. А работа ради работы», — сомневается собеседник издания.
Летом этого года «Русатом Имплантат», дочернее предприятие интегратора ТВЭЛ по направлению «Металлургия» «Русатом Металлтех», объявил о готовности выпускать 140 тыс. титановых имплантов (пластины для накостного остеосинтеза, штифты для лечения переломов и др.), а также хирургические инструменты. К концу 2024 года «Росатом» планирует занять не менее 30% российского рынка титановых имплантов.
Напомним, «Росатом» предложил создать центры аддитивных технологий (ЦАТ) на базе Уральского завода гражданской авиации (УЗГА), а в образовании — на базе КНИТУ-КАИ. Правда, пока этот вариант не окончательный, рассказывал «Реальному времени» Андрей Шевченко. По его словам, дорожная карта по формированию ЦАТ обсуждалась с раисом Татарстана и будет формироваться в течение этого года. Главный пункт в ней — формирование спроса на АТ и пакета заказов.
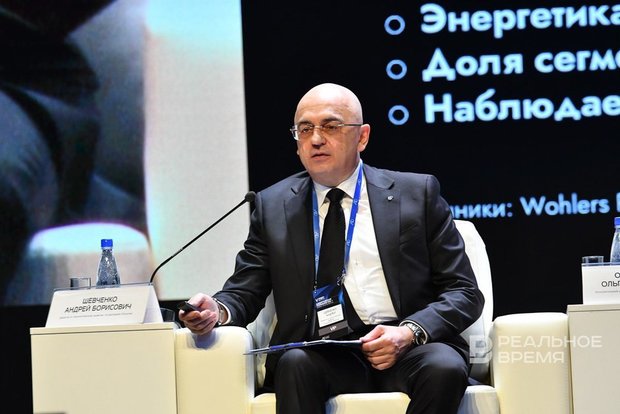
— Нам надо собрать руководителей предприятий и на их базе сформировать заказ. Что мы сделаем, сомнений нет. Мы не первый год работаем с республикой. Все построено, всегда выполняется в срок. Думаю, что мы подготовим карту с перспективой на 5—7 лет. То, что она получится, сомнений нет, — заключил он.
Подписывайтесь на телеграм-канал, группу «ВКонтакте» и страницу в «Одноклассниках» «Реального времени». Ежедневные видео на Rutube и «Дзене».